Lean Six Sigma for Services & BFSI
Revolutionize service delivery with AI-driven Lean Six Sigma
ASQ’s program merges AI with Lean Six Sigma to drive seamless operations and elevate customer experiences. Built on real-world case studies and AI-powered metrics, this course equips professionals to lead proactive, transformative change and deliver immediate, measurable impact in today’s digital service landscape.
Questions? We Can Help.
- Format : In-Person / On-site
- Duration : 48 Hours
Key Features of this course
- A.I Based Decision Making
- Interactive Sessions with Activities
- Expert trainers with Industry Experience
- Simulation Exams, Projects, Case Studies
- Real-World Simulations, Case Studies
- Aligned to ASQ's Global Standards
Services & BFSI - Industry Growth Potential
Master AI-Driven Strategies for Lasting Impact
AI Driven Tools
Capacity and Failure Analysis
Smart Performance
Optimizing Service workflow
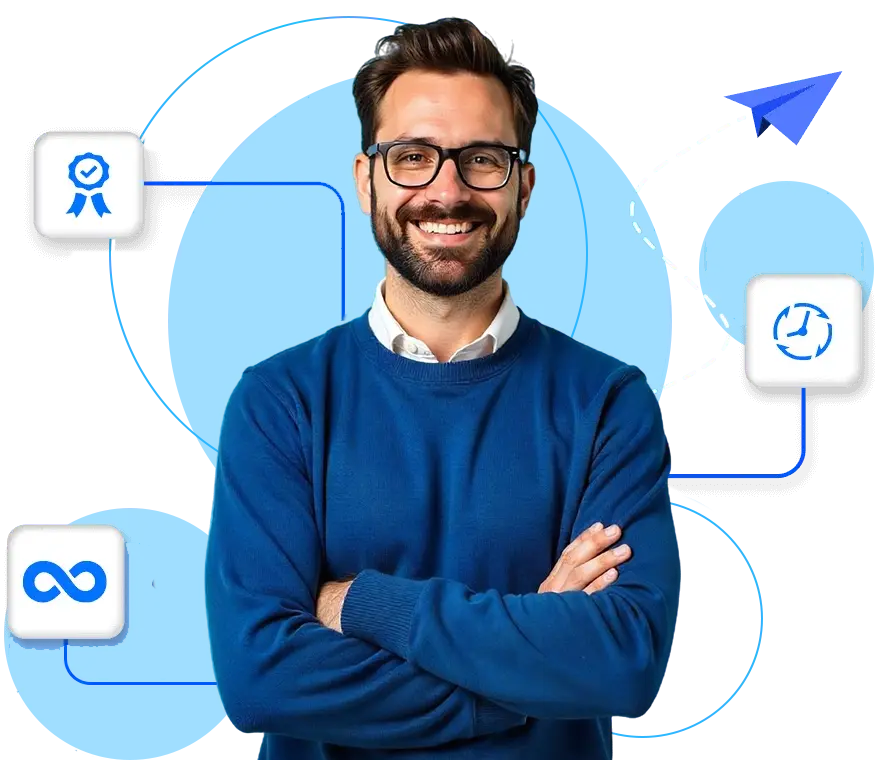
Project Management
Tailored to transactional operation
Continuous Improvement
For modern service environments
Join a Global Community of Certified Leaders
Certifications
400,000+
Countries
130+
Members
65000+
Communities
231+
This program goes beyond traditional Lean Six Sigma training by integrating advanced leadership principles with proven business improvement methodologies. The result? Leaders who can navigate complexity, drive change, and deliver measurable business outcomes.
Program Curriculam
Introduction
Lesson 01 – Introduction to Six Sigma
- In this lesson, you will explore the fundamentals of Six Sigma, its principles, and its role in achieving organizational goals.
Lesson 02: Six Sigma and Organizational Goals
- This lesson provides insights into the core concepts of Six Sigma, the DMAIC process, and the structure of Six Sigma teams, while linking them to organizational drivers and metrics.
Lesson 03: Lean Principles in the Organization
- Here, you will learn how Lean principles complement Six Sigma to enhance efficiency, reduce waste, and drive continuous improvement using key Lean tools and techniques.
Define Stage
Lesson 01 – Introduction to Define Phase
- In this lesson, you will be introduced to the Define Phase, setting the foundation for project identification and management.
Lesson 02: Project Identification
- Learn the critical steps in project selection, including benchmarking, best practices, and the SIPOC process, while understanding the roles of owners and stakeholders.
Lesson 03: Voice of the Customer
- This lesson focuses on identifying customers, collecting and analyzing VOC data, understanding Critical-to-Quality (CTQ) elements, and applying Quality Function Deployment to align customer needs with project goals.
Lesson 04: Project Management Basics
- Gain essential project management skills, including creating project charters, defining problem statements and objectives, interpreting project scope, and managing metrics, schedules, and risks effectively.
Lesson 05: Management & Planning Tools
- Explore advanced tools like affinity diagrams, interrelationship diagrams, tree diagrams, matrix diagrams, prioritization matrices, and process decision program charts to enhance planning and decision-making.
Lesson 06: Business Results for Projects
- Understand how to measure process performance using metrics such as Defects per Unit (DPU), Throughput Yield (TPY), Rolled Throughput Yield (RTY), Defects per Million Opportunities (DPMO), and Sigma Level.
Lesson 07: Team Dynamics and Performance
- Develop skills in team dynamics, including understanding team stages, roles, responsibilities, effective communication, and tools to enhance team performance.
Measure Stage
Lesson 01: Introduction to Measure Phase
- Begin the Measure Phase by understanding its purpose and significance in the Six Sigma methodology.
Lesson 02: Process Analysis and Documentation
- Learn how to analyze and document processes effectively using tools such as process maps, flowcharts, and comprehensive process documentation techniques.
Lesson 03: Probability and Statistics
- Explore the roles of probability and statistics in Six Sigma, including key concepts like addition and multiplication rules, permutations, and combinations.
Lesson 04: Collecting and Summarizing Data
- Master data collection and summarization techniques, including understanding data types, measurement scales, central tendency, dispersion, and visual tools like stem-and-leaf plots and box-and-whisker plots.
Lesson 05: Measurement System Analysis
- Gain insights into measurement system properties, characteristics, and concepts, and learn to conduct Gage R&R studies for both continuous and attribute data.
Lesson 06: Process and Performance Capability
- Understand process stability and normality, conduct capability analysis, and study performance indices to evaluate process mean shifts, variation, and attribute data capability.
Analyze Stage
Lesson 01: Introduction to Analyze Phase
- Understand the purpose and key objectives of the Analyze Phase in identifying and addressing process inefficiencies.
Lesson 02: Root Cause Analysis
- Learn to identify root causes of issues using the 7 Quality Tools and Root Cause Analysis (RCA) techniques.
Lesson 03: Failure Mode and Effect Analysis (FMEA)
- Explore FMEA methodologies, including types of FMEA, guidelines for implementation, and their role in preventing potential failures.
Lesson 04: Statistical Distributions
- Gain a deep understanding of statistical distributions, including binomial, Poisson, and normal distributions, along with foundational concepts like the Central Limit Theorem (CLT).
Lesson 05: Hypothesis Testing
- Master hypothesis testing fundamentals, including Type 1 and Type 2 errors, p-values, sample sizes, and statistical tests like T-tests, ANOVA, Chi-Square, and tests for non-normal data.
Lesson 06: Exploratory Data Analysis
- Learn to analyze data relationships through correlation, regression analysis, residual analysis, and linear regression techniques.
Improve Stage
Lesson 01: Introduction to Improve Phase
- Discover the goals and significance of the Improve Phase in implementing effective solutions to enhance processes.
Lesson 02: Design of Experiments
- Learn the fundamentals of DOE, including regression concepts, key terms, and understanding experimental error to optimize process improvements.
Lesson 03: Lean Tools
- Explore Lean tools and techniques to streamline processes, reduce waste, and enhance efficiency with methods like Value Stream Mapping (VSM), 5S, Total Productive Maintenance, and Kaizen.
Lesson 04: Selecting a Solution
- Master solution selection techniques, including Pugh Analysis, prioritization matrices, brainstorming, cost-benefit analysis, and piloting strategies to implement the most effective improvements.
Control Stage
Lesson 01: Introduction to Control Phase
- Understand the objectives of the Control Phase in maintaining and sustaining process improvements.
Lesson 02: Statistical Process Control (SPC)
- Learn SPC fundamentals, including control charts, their analysis, and selecting the right chart for data types, such as Xbar, I-MR, np, p, c, and u charts.
Lesson 03: Control Plan
- Develop skills to create effective control and response plans, conduct cost-benefit analyses, and understand KPIVs, KPOVs, and transactional control strategies.
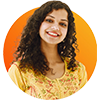
To fast-track your career, talk to a Learning Advisor.
- +91 11 46783399
Tools Covered
Projects Covered
Reducing Customer Onboarding Time
Simplify and streamline the customer onboarding process by eliminating redundancies, enhancing digital workflows, and improving first-touch resolution for faster account activations.
Improving Loan Processing Efficiency
Optimize loan approval workflows, reduce turnaround time, and improve accuracy by standardizing processes and integrating automation for better customer satisfaction and compliance.
Minimizing Service Request Escalations
Enhance first-call resolution rates by training staff, refining service protocols, and leveraging data analytics to address customer issues promptly and effectively.
- Soaring Demand and Accelerated Growth
Driving Operational Efficiency in a Service World
The biggest difference between manufacturing and transactional Lean Six Sigma lies in visibility and measurement. In manufacturing, the product moves physically through processes, guided by design. In contrast, transactional processes are often digital, making it harder to visualize workflow, waste, or variation—creating challenges in tracking progress and measuring outcomes.
This program fills that gap by tailoring Lean Six Sigma tools specifically for service and transactional industries. Participants will learn to identify bottlenecks, minimize waste, and streamline processes, ensuring measurable, real-world improvements.
Immediate application of these principles will drive career growth and deliver tangible organizational benefits through enhanced productivity, better customer experience, and reduced operational costs.
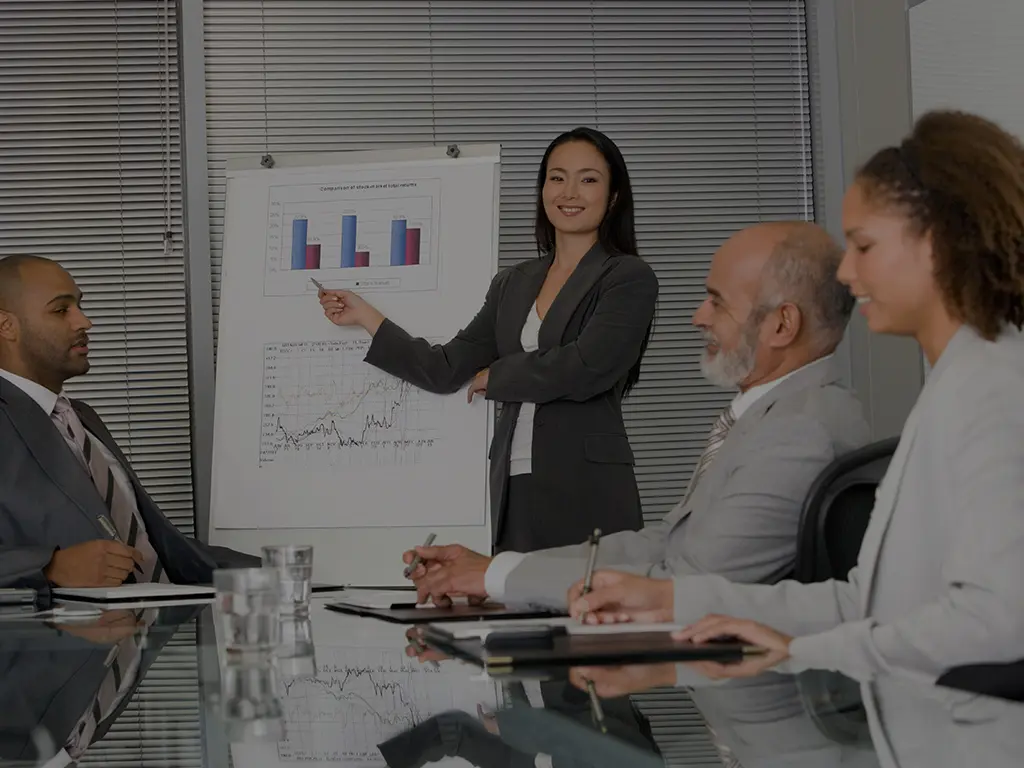
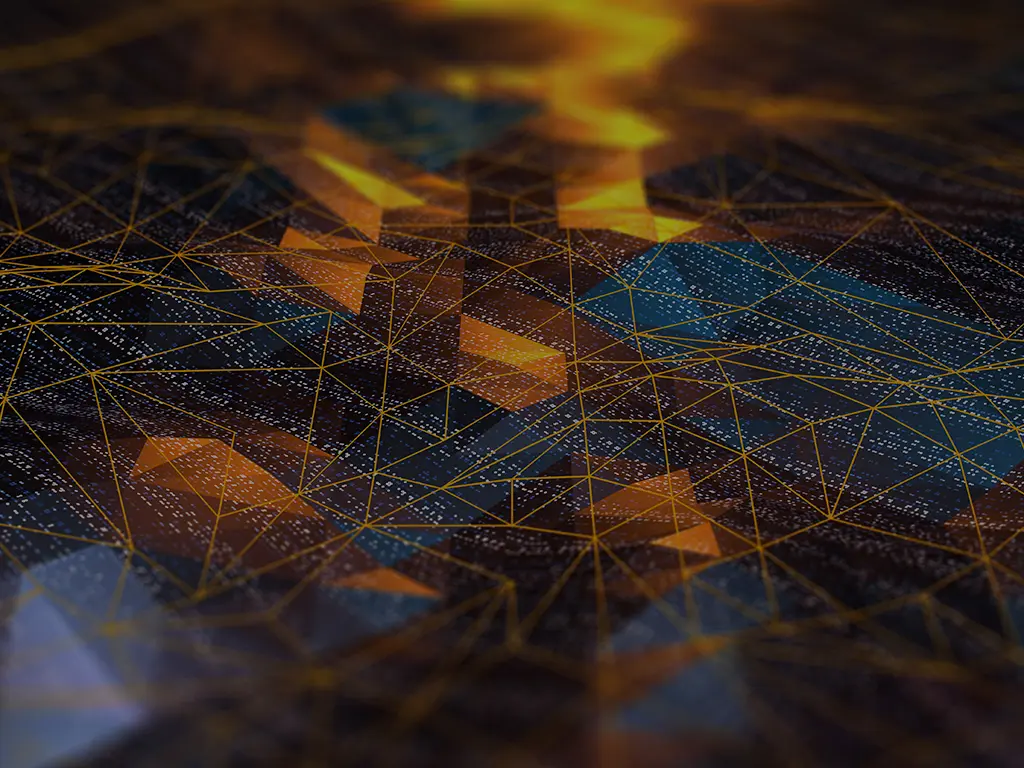
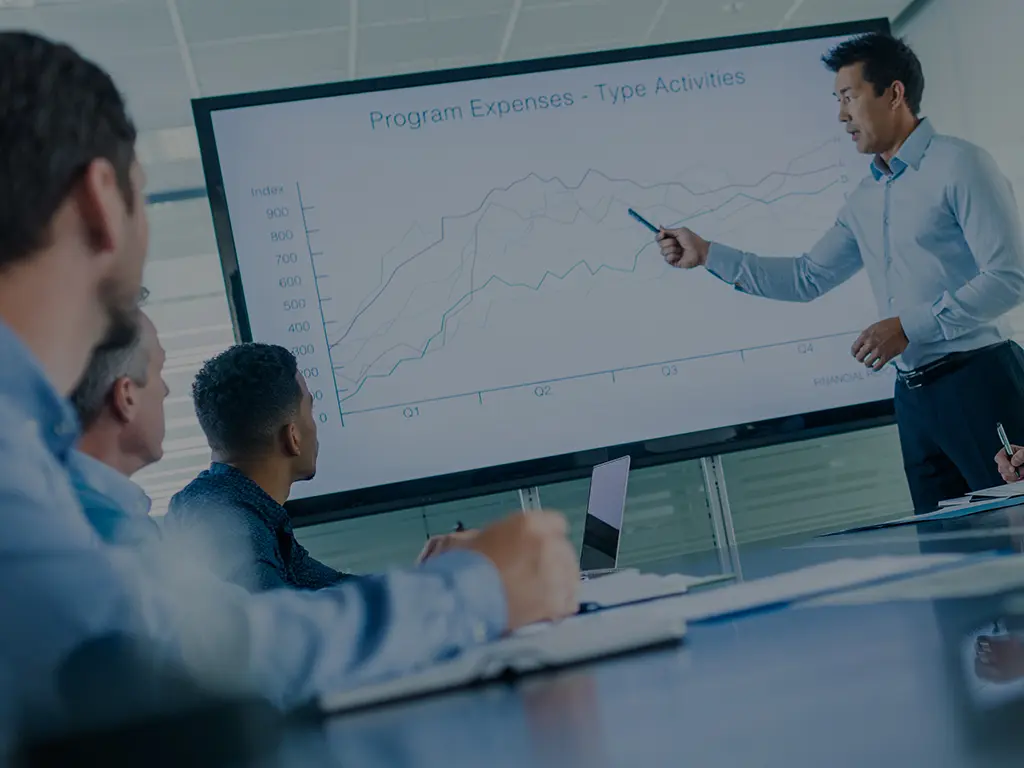
The ASQ ADVANTAGE
Expertise
Industry-tailored methodology developed by service operations experts
Innovation
AI-enhanced practical solutions drawn from successful digital transformations
Comprehensiveness
Comprehensive coverage from customer service to complex transactional workflows